Almost 80% of the world’s primary energy still comes from coal, oil, and gas, contributing heavily to global CO2 emissions and accelerating climate change. According to NASA and the IPCC (Intergovernmental Panel on Climate Change), the global average temperature is about to rise by 1.5 degrees C. This could lead to some devastating and widespread effects for our civilisation on this planet. Clearly, there is a pressing need to take action.
How green energy powers our operations
By strategically integrating renewable energy sources like solar and wind power, we are working towards a future where our factories are greener, more efficient, and less reliant on non-renewable resources.
This commitment has already led to several milestones. As on December 2024, we are proud to announce that 14 of our manufacturing sites have achieved 100% renewable energy status.
To be recognised as 100% renewable energy factories, our sites meet strict criteria such as Zero CO2 emissions from Scope 1 and 2 sources. Against our 2008 baseline, at Hindustan Unilever, we have achieved a reduction in total energy consumption by 45% (GJ/tonne of production).
How we are harnessing more and more renewable energy
Our green energy journey includes optimising both generation and consumption of energy. This dual focus enables us to maximise efficiency while integrating renewable energy sources.
Optimising electrical energy generation and consumption
We have installed 30 MW of solar panels across our factories, with another 1 MW under construction, and secured a 45 MW offsite solar project to further expand our capacity. On the wind energy front, we have a 10 MW windmill already in operation, with another 3 MW in development. Together, solar and wind accounted for 15% of our total electricity use in 2024, and this share will grow.
In addition to generating renewable energy, we are optimising how we consume it to further enhance efficiency. We are improving Energy consumption reduction by installing high efficiency motors, VFDs (Variable Frequency Drivers) to match actual demand of the load in conveyors and HVAC systems. Installation of Magnetic chillers consume 30% less electricity compared to conventional systems. Magnetic chillers operate without oil, which improves efficiency of overall system and reduce noise in the system.
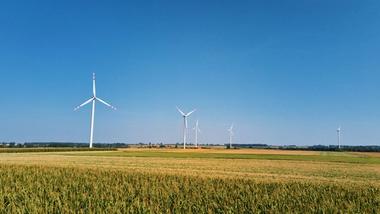
Optimising thermal energy generation and consumption
We have made significant strides in reducing our reliance on fossil fuels by introducing biomass fuels such as agricultural residues, bagasse briquettes, and organic waste to power our biomass boilers and thermic fluid heaters. By diversifying the types of biomass we use—like mango seeds and corn husks—we’ve successfully cut fuel costs by 12%, despite a 4% rise in biomass prices in 2024.
Our blend-flex fuel technology further ensures stability by allowing our boilers to operate with a variety of biomass fuels, providing flexibility and maintaining a low-cost energy supply.
Regarding thermal energy consumption, we’ve implemented condensate recovery systems that capture and reuse steam condensate, which holds up to 30% of the energy used in steam production. This helps lower both fuel and water costs. Additionally, our air distribution systems are optimised for reducing friction and air pressure, leading to a 7% reduction in energy use.
Separating high-low-pressure airlines has further reduced energy consumption and operational costs, making our thermal energy usage even more efficient. Electric boilers are crucial in driving the transition toward sustainable and low-carbon energy. The efficient and compact design supports our renewable energy journey by providing a clean, flexible, and efficient heating solution, significantly reducing reliance on fossil fuels. We have now started the integration of electrical boilers into our operations, further advancing our commitment to renewable energy and sustainability.
Industrial heat pumps play a vital role in advancing renewable energy adoption. By efficiently capturing waste heat and raising it to higher temperatures for industrial applications, they operate with minimal electricity consumption and utilise low-GWP refrigerants. These systems offer sustainable, energy-efficient, eco-friendly heating solutions, replacing traditional fossil fuel-based methods. We have integrated heat pumps into our operations, contributing to a significant reduction in energy consumption.
How our digital interventions are driving efficiency
We leverage advanced digital technologies to monitor and optimise our energy consumption in real time, enhancing efficiency across both thermal and electrical systems. Our digital twin technology creates virtual models of critical processes, such as boilers, allowing us to simulate and fine-tune operations to improve fuel efficiency and reduce energy costs.
For biomass boilers, digital twins can help improve fuel efficiency, reduce emissions, and enhance operational reliability. Integrating AI and machine learning enables better control over combustion processes, leading to more sustainable energy production.
Through our partnership with TCS, we’ve implemented the Clever Energy™ platform, an AI-powered system that delivers real-time insights into energy use, helping us make informed decisions that have already resulted in 5-6% reductions in energy costs. Moreover, our Real-time Visualisation & Analytics (RTVA) system tracks key equipment, such as boilers and compressors, allowing us to adjust settings and optimise performance for maximum energy efficiency. Together, these digital solutions ensure that our energy management is both proactive and efficient.
Achieving our green energy goals
Our focus on renewable energy generation, energy efficiency, and digital optimisation has already delivered impressive results.
At Hindustan Unilever Limited, sustainability is at the core of our mission. We are committed to using our resources responsibly, reducing emissions, and finding innovative ways to create a greener future for all.