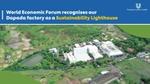
Hindustan Unilever Limited (HUL) today announced that its Dapada factory has been recognised as a Sustainability Lighthouse by the World Economic Forum (WEF).
This is the first Unilever site and the first company across sectors to achieve this status in India. This recognition comes on the back of the unit being accorded the designation of an advanced Fourth Industrial Revolution (4IR) Lighthouse earlier this year.
This additional ranking acknowledges existing Lighthouses that are trailblazers for the future of responsible manufacturing – sites that continue to push the boundaries of technology to create digitally enabled manufacturing processes that increase speed, agility and resilience, plus significantly reduce any impact on the environment.
Sanjiv Mehta, CEO and MD, HUL and President, Unilever, South Asia, said, "The Sustainability Lighthouse status reflects the use of revolutionary technologies, including digitally enabled manufacturing processes that have amplified speed and agility, and has lessened environment impact by reducing energy, water and material waste. The fact that this is not just the first Unilever site but also the very first Indian company to receive this recognition is a matter of pride and joy for all of us at HUL. Congratulations to the entire Dapada team."
HUL's Dapada unit has been recognised for its use of innovative solutions to act on Unilever's ambitious emission reduction targets (as outlined in Unilever's Climate Action Transition Plan), specifically the use of machine learning and integrated energy management systems to drive energy optimisation, and digital twin technology to accelerate eco-friendly formulations.
An independent expert panel at the World Economic Forum recognised the factory for implementing a series of advanced 4IR use cases, which are generating an impact on tangible metrics in sustainability.
Machine learning powered energy optimisation
One of the key initiatives was the deployment of Machine Learning on 1000+ manufacturing and energy parameters to identify critical parameters to reduce energy consumption while maximising productivity. A model was deployed on the production lines to auto-correct 80% of losses in real-time through predictions based on historical trends. This helped generate actionable insights for the process experts and line operators to correct the remaining 20% losses. The models were also integrated with weather forecasts and historical energy trends to suggest a production run strategy based on the week's plan to minimise energy consumption.
Faster & impactful eco-friendly formulation through Digital Twin
To create new formulations and get it first-time-right, a Digital Twin was developed using historical data and key influencers. The digital twin was deployed to map multiple and complex manufacturing aspects to launch formulations that score higher on the sustainability quotient. Similarly, through analytics, the Dapada team was able to identify critical process parameters to control quality and improve productivity.
As a result of these steps taken by the Dapada unit, the digital transformation on sustainability has been considerably superior.
The site has exceeded expectations, reducing energy consumption by 48%, material waste by 35% and water consumption by 36%.
Francisco Betti, Head of Shaping the Future of Advanced Manufacturing and Value Chains, WEF, said, "Global disruptions have highlighted the fragility of current supply chains – as rising inflation, and material shortages are increasing pressure on manufacturing organisations, Lighthouses show that scaling the deployment and adoption of Fourth Industrial Revolution technologies across multiple factories and business functions is key to accelerate the achievement of their strategic imperatives, such as business growth, resilience and greener operations."
The Global Lighthouse Network:
The Global Lighthouse Network is a community of production sites and value chains that are world leaders in the adoption and integration of the cutting-edge technologies of the Fourth Industrial Revolution (4IR). Lighthouses apply 4IR technologies such as artificial intelligence, 3D-printing and big data analytics to maximise efficiency and competitiveness at scale, transform business models and drive economic growth, while augmenting the workforce, protecting the environment and contributing to a learning journey for all-sized manufacturers across all geographies and industries. The Global Lighthouse Network is a World Economic Forum project in collaboration with McKinsey & Co, factories and value chains that join the Network are designated by an independent panel of experts.